AIGC为制造业创造的三大价值:行业know-how快速转化成企业自身能力、突破人工经验局限形成新能力、数据和知识不出厂。5月23日,36氪举办“颠覆·AIGC”产业发展峰会。本次峰会汇聚产业力量,共同探讨企业、行业在面临变革时的应对策略,分享思考,探索和发现产业中最具潜力的企业与最具价值的技术,在激荡的环境中探寻前行的方向。
大会上,洪朴总裁陶青发表了题为《基于AIGC的制造业知识管理》的主题演讲。基于洪朴利用AI大模型赋能制造业企业的三个具体案例,陶青分享了AIGC为制造业创造价值的三种途径:一是,基于AIGC,制造企业可以全面继承在行业内长期积累的知识,将行业know-how快速转化成企业自身能力;二是,制造企业可以对分散在各个系统、文档、数据库、流程制度中的、各个专业领域的知识,进行综合分析和理解,突破人工经验局限,形成新能力;三是,制造企业可以将有价值的数据、经验留存在企业内部,而不是“随人而动”,可以提升对知识的保护力度。
制造业场景繁多,不同行业又涉及不同细分场景。陶青指出,洪朴过去的做法是针对性解决不同场景、行业分别面临的智能数据分析问题,但在AI大模型出现后,正在探索如何基于新的技术糅合多场景数据,实现制造企业的全局知识管理。
以下为陶青演讲实录(经36氪整理编辑):
大家好!
站在时代面前我们会有非常多的机会,接下来我分享一下我们的观点和故事,我是陶青,来自洪朴,我们致力于让AI惠及中国制造。
我不是做技术出身,我从行业起步,在半导体从业了10余年,接下来我将分享三个故事,与大家一起探讨AIGC技术能为制造业带来什么价值。
第一个故事,我想称之为“后发优势”的故事。这个故事是关于半导体行业中的一类常见设备,其国产化的时间已经不短了。客户告诉我们这类设备国产化后故障率相对较高,控制精度也不是很好。我们是做制造业数据分析服务的,设备控制和设备诊断是我们的主要场景,我们发现这可能是中国制造业设备国产化的一个重要话题。中国开始有越来越多的国产化设备,特别是在高端制造,譬如半导体行业中,我们已经有了很多国产化的高端设备。但可能设备是国产的,控制参数是海外引进的,我们还没有足够的时间完全掌握这些设备。这也是我们中国在制造业发展过程中必须要经历的过程。
那这样的情况给我们客户带来了什么样的具体问题呢?我们看到客户的设备工程师在一边研究材料学的论文,一边研究如何调试设备参数;他们缺乏此类设备的使用经验,所以这些控制参数到底为什么要这样设置?这项参数为何是30,而不是50?那项参数为何是35.5,而不是35.4?这些经验,我们本土工程师是不具备的;但这个设备却有多达854个变量,复杂程度已经远超人的能力,客户工程师不可能筛选出最优的变量组合。
于是我们从客户手里拿到了这类型设备的各类数据,比如参数、指标、日志信息、生产过程中操作数据等,我们还拿到一些客户手上的海外同类型设备文件资料。经过学习、分析和模型的适配后,我们为客户提供了一套参数优化系统,图片上隐去了一些敏感推荐参数(图1),系统会分析客户每次生产的变化,原材料变化、生产环境变化、设备PM变化,对每一次变化都进行生产参数推荐。
图1:参数优化系统(IDA智能数据分析系统) 企业供图从第一次拿到数据,到最后形成参数推荐,大约用了两个月的时间,根据每一次参数推荐我们都会做一次实验,直到发现这样一个变化(图2):蓝色柱状图是经过优化之后明显提升的生产数据,这个数据已经达到国外同类型设备的品质,我们对于数据的优化情况感到非常惊喜。从这个小故事中,我们学到了第一个认知:基于AIGC,制造企业可以将行业长期积累的知识,全面的继承和学习,快速转化成企业自身能力。这是我们认知到第一个点。
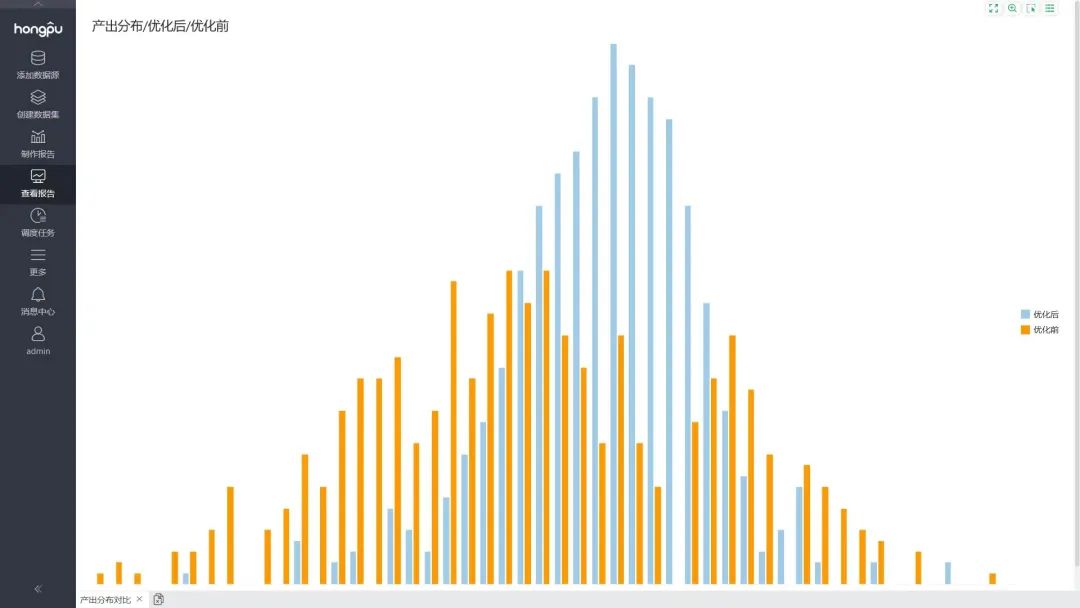
第二个故事,我称之为 “智能拐点”,这也是我们的真实故事,关于我们的一个半导体客户。该客户的一个生产基地有4个工厂,几百道生产工序,几千台设备,几十类产品,这意味着在中国,这个基地可能是该行业中最先进的。这个工厂的领导在和我们交流的过程中,向他们自己的工程师进行了提问:你们分析数据的时候,大概有多少数据量?工程师计算后表示,大约有几百道工序,一个电性能参数可能会有十几万个控制变量,一个产品有几十个电性能参数,数据量庞大。而且我们有几十类产品,如果这几十类产品同时生产,大约有几十亿、甚至上百亿的控制变量需要交叉控制和分析。领导提出了第二个问题:人工能做到吗?工程师表示这是不可能的。他们只能去抓取一些关键的指标,做一些定性的分析,远不能做到定量,并且只能是今天抓取数据,明天做好分析,后天再来看报告。这就是国内该行业最领先企业的现状。
我说洪朴或许可以尝试着来解决这个问题,于是我们基于AIGC技术给这个企业提供了IDA系统(智能数据分析系统),结论非常明确:数据分析效率提升11倍,发现生产线问题或者故障的周期缩短了95%。各位看到这个表现会觉得其实还行,这也是大数据时代的常规表现。这个故事名字大家还记得吗?我称之为“智能拐点”,拐点在什么时候出现呢?
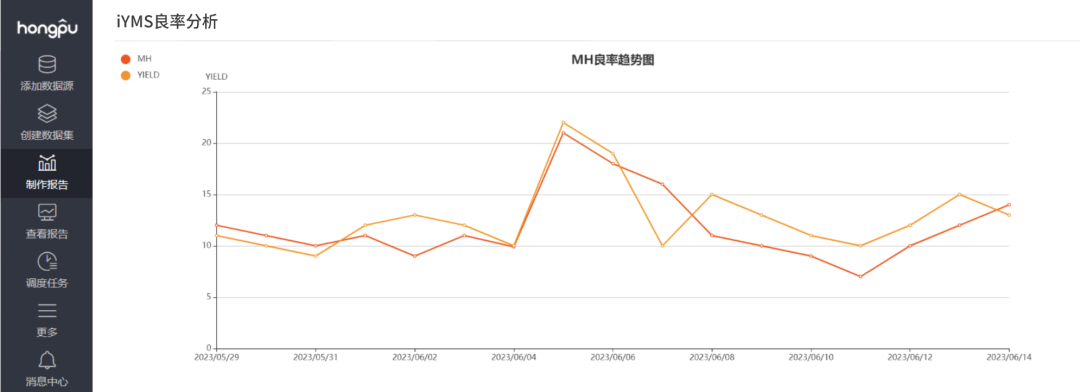
图3:MH参数对产品电性能表现的影响 企业供图
有一次和这个领导开会,我们分享了一个发现,如图3所示,不难看出有一项参数对于某款产品的最终性能有直接负面影响,这位领导问了一个负责人:这个说法准确吗?这个负责人说:这是我们没有考虑到的,我们不知道有这样一项影响因素。于是我们做了几次实验,证实这个影响确实存在。
这个领导又问技术负责人:你们原先的企业是这么做的吗?这个负责人说:不是,当时我们也不知道有这个问题存在。听完工程师的答案后,领导表示他此时已经相信IDA系统的智能性了。所以我们说这一天是智能拐点的节点。
这个故事让我们又得到了一个新的认知:基于AIGC,制造企业可以将分散在各个系统、文档、数据库、流程制度等各个专业领域的知识进行综合分析和理解,突破人工经验局限,形成新能力。
第三个故事更有意思。光伏是近几年的热词,我们在光伏行业有很多客户和成绩。光伏的某主要设备大约每三年会有一次重大更新,所以这个设备的工程师炙手可热,对于各个大厂而言都很抢手,这也导致这个设备的工程师跳槽频繁,薪资涨幅高达50%之多,因此导致光伏企业不敢深入培养工程师,企业担心把主要知识和工艺经验告诉工程师后,虽然设备维修的问题解决了,但万一跳槽该如何是好?所以这是一个很矛盾的问题,我称之为“熊掌和鱼”的故事。
一方面是企业缺少成熟工程师,另一方面企业又不敢给他们培训。我们提供一套系统,整合企业在这套设备上的各类数据:生产数据、质量图像数据、设备的日志信息、mes数据等等,我们将这些数据综合起来训练,并通过洪朴的“设备哨兵系统”对设备实时管理,一段时间后我们看到:良品率、物料损耗、维护时长、人员效率等各方面指标都有明显的提升,从而实现降本增质。当然更为显著的益处在于客户的数据将被留存在企业内,同时帮助更多的产线员工具备专家级别的设备维护能力,这也是AIGC为制造业带来的价值。
做一个总结:洪朴对于AIGC在制造业知识管理上面能为行业带来什么价值?我们能带来以下三点价值。
第一,知识继承,不管知识是海内外的,还是留存百年的,只要有数据或是一些能够被阅读的内容,技术和模型能够将它转化为企业的能力;
第二,经验突破,我们能挖掘出一些人工无法发现的问题,这些问题处在经验盲区。当所谓多模态、多交叉学科的知识汇聚时,一定会有有不一样的发现,这是通过人工无法实现的。
第三,知识保护,我们能把数据留存在企业内部,我们称之为数据不出厂,知识不出厂。
制造业还有很多很多场景,刚才说到设备故障诊断,工艺参数优化,还包括APS、EHS管理、生产流程整合、质量分析等等,不同行业中也有很多不同细分场景,比如半导体、光伏、汽车钢铁等。
我们在不同场景和不同行业研发、落地、完善我们的产品,但是AIGC的概念和技术出现之后,我们在思考,如果打通各类场景的所有数据会怎样?AIGC是不是可以在这样一个十分垂直的行业中,甚至在对于数据安全很敏感的制造企业中,能很好的管理这个制造企业的全局知识,让问题从一边输入的同时,好的解决办法就能从另一边输出呢?我们很期待。最后,让我借用上午韦青总的话来结束今天的分享:让我们把一些难的、复杂的或者是不想做的事情,交给算法,让我们人类继续进化。
谢谢大家,我是陶青,我来自洪朴。

